Vaillant Boilers
Do You Need A Vaillant Boiler Engineer In Maidstone?
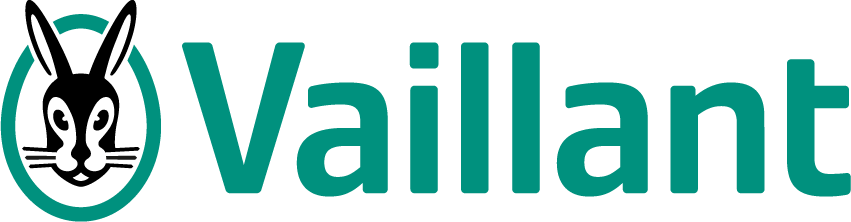
The Only Vaillant boiler engineer in Maidstone
As a previous employee of Vaillant, Kevin spent 3 years working for Vaillant’s Technical Department located in King’s Hill
My role at Vaillant in Maidstone, was to advise fellow Gas Safe Registered Engineers on how to fix and install Vaillant Boilers and products. Being located in a training centre also allowed me to undertake all courses offered by Vaillant, as well as the huge amount of training I was given to become an expert in their products, so I could offer technical advice to Gas Engineers.
Information about Vaillant Boilers
Vaillant boilers are well known for lasting many years. There are still many VCW models in circulation and approximately 30 years old.
Vaillant also manufactures parts for 15-20 years unlike other manufacturers like Ideal who have been known to cease production of components that are just 9 years old resulting in a new boiler being required should that part fail.
Vaillant, are superb boilers and being German designed, it encapsulates German engineering prowess and is Manufactured in Derbyshire, England.
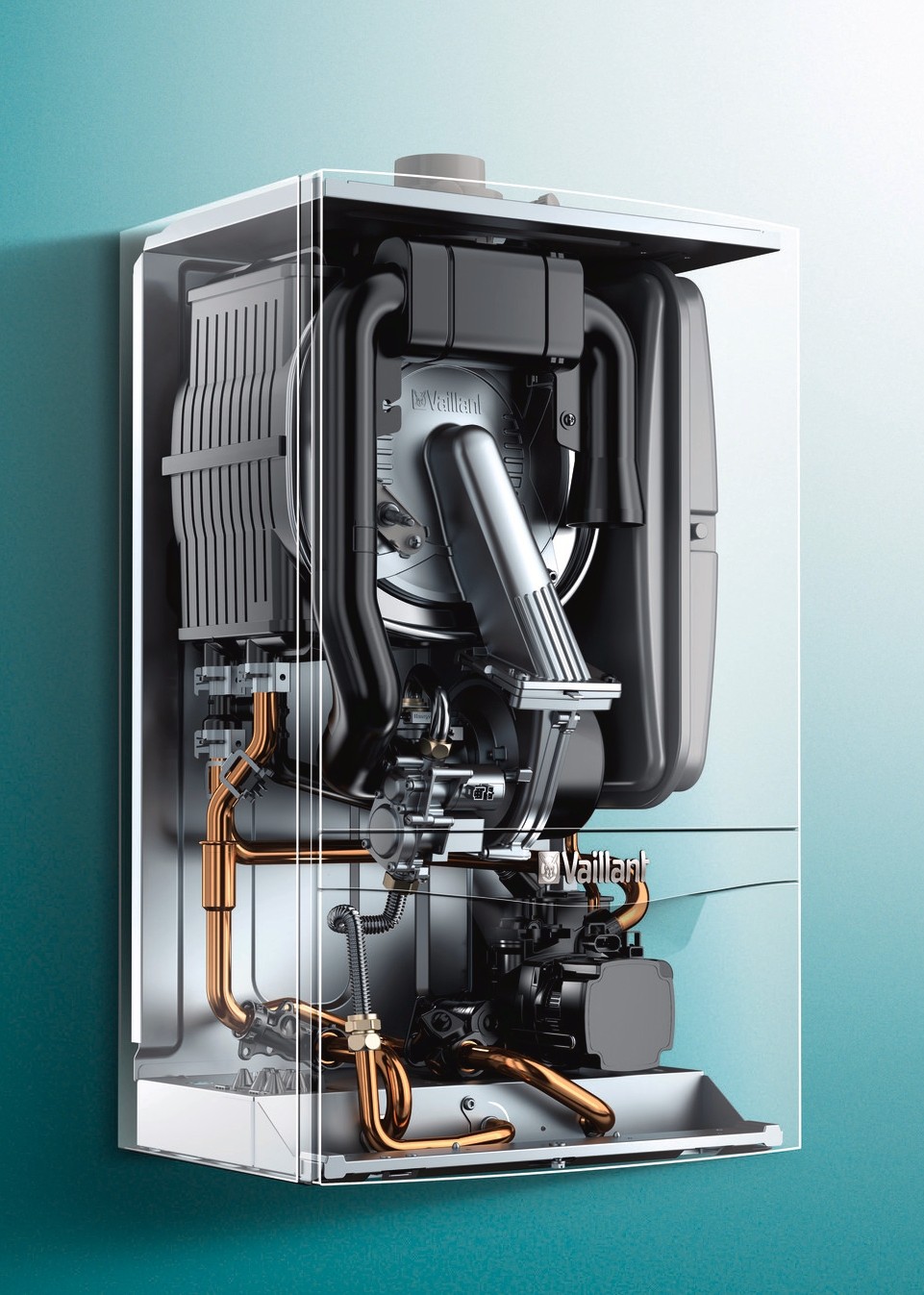
Vaillant boiler engineer in MaidstoneCommon Vaillant Boiler Fault Codes and How to Fix Them
Vaillant boilers are renowned for their reliability and efficiency, but like all complex systems, they can experience occasional issues. Modern Vaillant boilers are equipped with diagnostic tools that display fault codes when something goes wrong. These codes provide an indication of the problem, helping homeowners and technicians diagnose and resolve issues quickly. Below is an overview of the most common fault codes associated with Vaillant boilers and practical advice on how to address them, some issues require a Vaillant boiler engineer in Maidstone.
F22 – Low Water Pressure
Cause: This fault code indicates insufficient water pressure within the boiler system, which is critical for safe and effective operation. It’s one of the most common issues homeowners encounter.
Solution:
Check the boiler’s pressure gauge. If the pressure is below 1.0 bar, it’s too low.
-
Locate the filling loop, typically found beneath the boiler, and use it to add water to the system. Open the valves carefully and watch the pressure gauge.
-
Once the pressure reaches 1.5 bar, close the valves.
-
Reset the boiler to clear the fault code.
If the pressure continues to drop, there may be a leak in the system or a problem with the pressure relief valve, requiring a Vaillant boiler engineer in Maidstone.
F28 – Ignition Failure
Cause: The boiler has failed to ignite, which could result from issues such as insufficient gas supply, blocked burner, or a faulty ignition system.
Solution:
-
Check if the gas supply is on and functioning correctly. Ensure no disruptions in the gas supply from your provider.
-
Inspect the condensate pipe for blockages, especially in cold weather, as it might be frozen.
-
Reset the boiler and attempt to ignite it again.
If the issue persists, it may indicate a fault with the ignition electrodes, gas valve, or PCB, all of which require the expertise of a Gas Safe registered engineer.
F75 – No Pressure Change Detected
Cause: This code indicates the boiler’s pump or pressure sensor is malfunctioning. It’s commonly associated with a faulty pump, airlocks, or issues with the pressure sensor.
Solution:
-
Check the boiler’s water pressure to ensure it is at the correct level.
-
Listen for unusual noises from the pump, which might indicate an airlock or failure.
-
Bleed the radiators to release trapped air in the system.
If the pump or pressure sensor is defective, a professional will need to replace it, but as a temporary measure, incresing the pressure to 2/2.5 may work whilst waiting for an heating engineer / a Vaillant boiler engineer in Maidstone
F29 – Flame Extinguished During Operation
Cause: The burner flame goes out unexpectedly during operation, often due to issues like unstable gas pressure, blockage in the flue, or a faulty flame sensor.
Solution:
-
Check the gas supply and ensure it’s stable.
-
Inspect the flue for obstructions or blockages, like plants or leaves.
-
Reset the boiler and observe if the fault recurs.
If the problem persists, a Vaillant boiler engineer in Maidstone who is a Gas Safe engineer should inspect the flame sensor and gas valve.
F32 – Fan Fault
Cause: This fault indicates an issue with the fan, which is crucial for expelling flue gases and ensuring proper combustion. A defective fan or wiring issue is often the cause.
Solution:
-
Inspect for any visible damage or loose connections around the fan. (only possible by a Registered Gas Safe Engineer.)
-
Reset the boiler and see if the fan operates correctly.
Replacing the fan or repairing electrical faults should be performed by a qualified technician.
F54 – Flame Signal Interrupted
Cause: This code points to an intermittent flame signal caused by low gas pressure, flue blockages, or a defective flame rectification electrode.
Solution:
-
Check the gas supply and flue for any issues.
-
Reset the boiler to clear the fault.
For ongoing issues, a professional inspection is needed to diagnose and repair the flame detection system, you will need the experience of a Vaillant boiler engineer in Maidstone.
F61 – Gas Valve Fault
Cause: A fault in the gas valve or its connections can trigger this code. It often involves a short circuit or mechanical failure of the valve.
Solution:
-
Turn off the boiler and inspect the connections to the gas valve. (Gas Engineer only)
-
Reset the boiler and attempt to restart it.
If the fault persists, the gas valve may need replacing by a Vaillant boiler engineer in Maidstone.
F62 – Delayed Ignition
Cause: Delayed ignition can occur due to a defective gas valve, ignition electrodes, or insufficient gas supply.
Solution:
-
Check the gas supply to ensure it’s adequate.
-
Reset the boiler and monitor its operation.
A Gas Safe engineer, specifically a Vaillant boiler engineer in Maidstone will inspect and repair components like the gas valve or ignition system if the problem continues.
F70 – Invalid Boiler Configuration
Cause: This fault occurs when the boiler’s internal settings or components do not match its configuration, often after installation or maintenance.
Solution:
-
Reset the boiler to attempt clearing the fault.
-
Review the configuration settings, which may require professional tools and expertise.
Consult a qualified Vaillant boiler engineer in Maidstone to ensure the boiler’s settings align with its installed components.
F76 – Overheating Heat Exchanger
Cause: Overheating of the heat exchanger is often caused by limescale buildup, inadequate flow, or a faulty temperature sensor.
Solution:
-
Check for adequate system pressure and flow.
-
Flush the system to remove limescale and debris.
-
Reset the boiler to clear the fault.
If overheating persists, a technician may need to replace the temperature sensor or clean the heat exchanger.
General Maintenance Tips to Prevent Fault Codes
-
Annual Servicing: Regular servicing by a Gas Safe registered engineer can identify potential issues before they become critical.
-
Check Pressure Regularly: Keep the pressure within the recommended range (1.0-1.5 bar).
-
Bleed Radiators: This prevents airlocks and improves system efficiency.
-
Protect Against Freezing: Insulate the condensate pipe and ensure your boiler is in a frost-protected location.
-
Monitor Performance: Pay attention to unusual noises or performance drops and address them promptly.
By understanding and addressing these common fault codes, you can ensure your Vaillant boiler remains efficient, reliable, and safe. For complex issues, always consult a qualified professional to avoid compromising the boiler’s performance or safety. KMC Gas is the only Vaillant Engineer in Maidstone and we can offer unrivalled experience to repair you Vaillant boiler